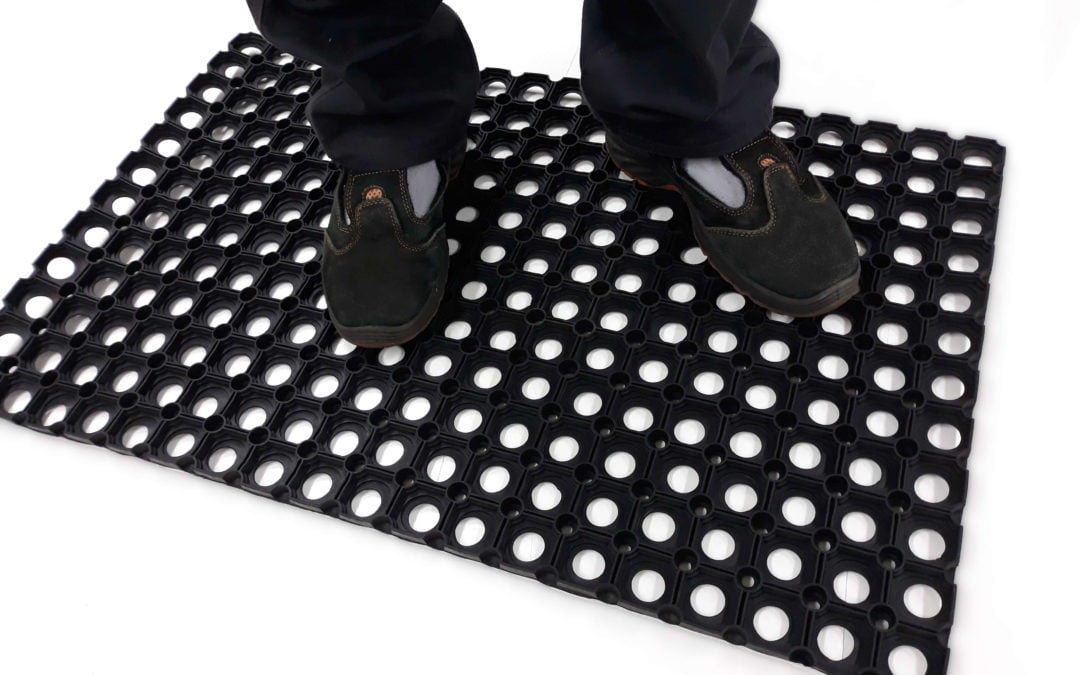
Historia gumowej wycieraczki
Wycieraczka jaka jest każdy widzi. Ot, zwykły kawałek gumy, położony przed każdymi niemal drzwiami wejściowymi na świecie.
Ale przyznaj, kimkolwiek jesteś, czy właścicielem firmy, który poprawia gumową wycieraczkę przed swoimi drzwiami każdego poranka wchodząc do firmy, czy klientem kawiarni, który oczekując na zamówienie podziwia wyszukany wzór na wycieraczce przed drzwiami lokalu który odwiedza, każdemu z nas, no prawie każdemu, przyszły do głowy te pytania: Wycieraczki. Skąd się wzięły? Kto je wymyślił? Skąd pochodzą?
Kto pyta nie błądzi! Usiądź wygodnie, bo o to przed Tobą kilka słów właśnie na ten zaniedbywany temat. Krótka historia Jej wysokości – Wycieraczki.
Archeolodzy przypuszczają, że pierwsze „przenośne nakrycia podłogi” były wykonane 25 000 lat temu w czasach paleolitycznych. Dawne klany, na potrzeby własne lub ściślej na potrzeby swoich siedzib, wykonywały wycieraczki z kory drzewnej. Z kory uzyskiwano rodzaj materii podobnej do filcu, z której następnie powstawały wycieraczki.
Nawet ludzie żyjący w bardzo odległych czasach, nie lubili widocznie, gdy do ich domów wnoszono brud, czy krew upolowanych zwierząt.
Niedługo później, ludzie zaczęli rozwijać praktyczną umiejętność jaką jest tkactwo. Zadanie to, spoczywało początkowo wyłącznie na barkach kobiet, które używając głównie słomy lub traw, tkały zarówno ubrania, jak kosze i inne przedmioty. Pierwsze potwierdzone użycie tkanej maty jako wycieraczki miało najpewniej miejsce w Mezopotamii około 6 000 lat temu.
W czasach biblijnych, ludzie niezamożni, których domy posiadały glinianą podłogę, używali mat jako posłania, a nie jak dziś do wycierania butów. Te maty, protoplaści dzisiejszych wycieraczek, były najprawdopodobniej wykonywane z przędzy wełnianej. Tego rodzaju nakrycia podłogi były popularne aż do czasów Średniowiecza.
W Japonii, lokalna szlachta wykorzystywała maty tatami już w wieku dziewiątym. Tatami to mata wykonana ze słomy, zarówno ryżowej jak i z sitowia. Miejsca nakryte takimi matami, były zarezerwowane jako te, z których mogli skorzystać tylko i wyłącznie arystokraci. Aż do wieku siedemnastego, maty te nie były dostępne dla plebsu i nie były używane w domach ludzi tzw. gminu.
We wczesnych latach wieku dziewiętnastego, produkcja protoplastów wycieraczki gumowej wkroczyła na nowe tory. Wycieraczki zaczęto wówczas wytwarzać z odpadów, które powstawały w warsztatach tkackich. Resztki przędzy pozostałe na krosnach były wykorzystywane do tego, by wpleść je w konstrukcję bazową, powstałą w oparciu o słomę lub inny, sztywny materiał. Ta metoda (której źródła sięgają być może jeszcze bardziej odległej historii), zwana wyplataniem dywaników, stała się popularna w Anglii i upowszechniła wyplatane wycieraczki w Anglii oraz innych krajach.
Wraz z nadejściem wieku dwudziestego, lista materiałów stosowanych do produkcji wycieraczek znacznie się wydłużyła. W Ameryce, ludzie wykorzystywali wszystkie materiały począwszy od słomy i juty aż po płótno do ich wytwarzania. Dopiero w czasach Rewolucji Przemysłowej, zaczęto powszechnie pokrywać podłogi matami powstałymi z mieszanek gumowych. Obecnie, wycieraczki nie tylko służą do utrzymania czystości, ale także są często produktami ekologicznymi. Wiele z nich, produkowanych jest z odzyskanych materiałów plastikowych, takich jak butelki, opony, etc. Nowoczesne wycieraczki gumowe mogą też stanowić element wyposażenia wnętrz i być bardzo atrakcyjne wizualnie. Wycieraczki mogą przez lata zachowywać wysokiej jakości nadruki na swojej powierzchni, dzięki nowoczesnym technologiom druku. Współczesne wycieraczki mogą też posiadać wiele funkcji specyficznych. Mogą to być takie funkcje jak: podwyższone wchłanianie wilgoci, intensywne oczyszczanie butów z błota i gliny, czy nawet redukowanie zmęczenia tych, którzy je użytkują.
O wycieraczce. Do czego nam ona?
W kilku bardziej naukowych słowach wycieraczka to system czyszczący, którego celem jest zatrzymanie zanieczyszczeń przenoszonych głównie na butach i niedopuszczenie do wniesienia ich do wnętrza budynku. Gumowy, metalowy lub inny fragment wybranej materii, umieszczany przed drzwiami wejściowymi każdego typu pomieszczeń1. Kto by pomyślał – kawałek gumy – a już okrzyknięty „systemem”.
Nasza bohaterka, wykonana z różnych materiałów, najczęściej gumowa, czasem tekstylna, z włókien naturalnych lub syntetycznych, rzadziej mosiężna lub z innych materiałów, ma za zadanie bronić naszych pomieszczeń przed zabrudzeniem.
Wycieraczkę cechuje, poza jej nadrzędną czyszczącą rolą, trwałość i odporność na działanie niesprzyjających warunków atmosferycznych. Cóż, trwałość bywa często sprawą dość umowną nie tylko w odniesieniu do wycieraczek…
Wycieraczka jest najczęściej prostokątna, spotykane bywają także o innych kształtach. Ich rozmiar zależy od typu pomieszczenia przed którym są położone. Wiele firm zamawia indywidualnie specjalne wycieraczki, wyposażone w szczoteczki czyszczące, które mogą układać się w logo danej firmy lub inne wzory graficzne. Druk na różnorodnych podłożach umożliwia ozdobienie każdej wycieraczki w najbardziej wymyślny i unikatowy sposób.
Budynki wielorodzinne wyposażone są często w jedną wycieraczkę przed wspólnym wejściem (zazwyczaj jest ona wykonana z metalu i trwale wbudowana w podest przed wejściem do danego budynku), a przed drzwiami poszczególnych mieszkań ułożone są indywidualne wycieraczki należące do poszczególnych lokatorów2.
Polski akcent – pierwsze wzmianki
W Polsce, jednym z wiodących producentów wyrobów gumowych, jest Zakład Przemysłu Gumowego „Stomil” S.A. z Bydgoszczy.
Jak czytamy w dostępnych materiałach, w roku 1937 nastąpiło pewne ożywienie gospodarcze, a co za tym idzie w „Stomilu” wprowadzono do produkcji nowe wyroby, takie jak wykładziny podłogowe, wycieraczki do obuwia, rozwinięto także produkcję innych wyrobów gumowych.
Na polskiej mapie produkcji mat i wykładzin gumowych swoje piętno odcisnęła także Warszawsko – Ryska Fabryka Wyrobów Gumowych „Rygawar” zlokalizowana na warszawskiej Pradze, gdzie w latach 1936/ 37 produkowano między innymi kalosze, obuwie gumowe, śniegowce i tkaniny gumowe5.
W podobnym kierunku rozwija się firma „Sanok”, znana ze swoich marketingowych ekstrawagancji, umiejscowiona w ówczesnym województwie lwowskim. Organizuje ona loty balonem, którego powłokę wykonano w fabryce w Sanoku. W 1936 roku firma posiada również wyłączną licencję angielską na gumę porowatą z lateksu oraz produkuje m.in. płyty posadzkowe i chodnikowe oraz tkaniny gumowe różnego zastosowania6.
Styl i moda a wycieraczki
Na koniec kilka słów o modzie i skutecznych rozwiązaniach jeśli chodzi o dobór wycieraczek do wnętrz.
Według specjalistów, kolorowa i fantazyjna w kształcie wycieraczka to wizytówka zadbanego i modnego domu. Kiedy kończy się sezon jesienno-zimowy a z nim czas pluchy, błota i mokrego śniegu, wycieraczka jest najczęściej bardzo zużyta i należy ją wymienić na nową. Jednocześnie nadejście wiosny i lata nie oznacza w naszym klimacie braku opadów i słot7.
Praktyczna i modna wycieraczka przed drzwiami domu czy mieszkania, nie tylko chroni podłogi wnętrz, wydłuża ich żywotność, obniża koszty sprzątania w instytucjach oraz zwiększa bezpieczeństwo (ryzyko pośliźnięcia się na mokrej podłodze). Ostatecznie, a może przede wszystkim, zdobi wejście i przyciąga uwagę.
Wycieraczkę możemy zatem dobierać nie tylko odpowiednio do stylu naszego domu czy mieszkania, ale także do pory roku. Niemniej, ważny jest też aspekt praktyczny.
Wybór wycieraczki zależy między innymi od intensywności jej używania – przed wejściem do biura, restauracji czy innego lokalu, konieczne jest zastosowanie bardzo wytrzymałych wycieraczek. Ważne jest także czy wycieraczka ma znajdować się przed mieszkaniem na klatce schodowej, czy przed drzwiami domku jednorodzinnego.
Wycieraczki wewnętrzne są przeznaczone do klatek schodowych, zamkniętych przedsionków i zadaszonych wejść, gdzie nie są narażone na zamoknięcie. Asortyment ich jest bardzo szeroki:
Wycieraczki kokosowe to jedna z propozycji do miejsc osłoniętych przed opadami. Dobrze chłoną wilgoć a duże zagęszczenie włókien oczyści dokładnie nasze obuwie. Są produkowane w znacznej ilości wzorów i kształtów, bo łatwo podlegają obróbce, tj. barwieniu i cięciu. W zależności od preferencji właścicieli nieruchomości, można wybrać wycieraczkę z zabawnym napisem, przywitaniem, wesołym rysunkiem lub z innym motywem. Są też dostępne wycieraczki okolicznościowe nawiązujące do wydarzeń, świąt lub danej pory roku.
Wycieraczki podgumowane na spodzie z wierzchem poliamidowym lub polipropylenowym i bawełnianym, dobrze przylegają do posadzki, nie przesuwają się a więc jednocześnie dobrze chłoną wodę i gwarantują bezpieczeństwo. Takie wycieraczki można prać w pralce.
Wycieraczki do zastosowań zewnętrznych, muszą być wyjątkowo wytrzymałe i odporne na działanie zmiennych warunków atmosferycznych. Przed wejściem do domu, segmentu, czy budynku użytku publicznego odpowiednie będą wycieraczki ażurowe, które z powodu swojej budowy nazywane są „plastrami miodu”. Zrobione są z wymiennych, trudnościeralnych gumowych szczotek i efektywnie czyszczą obuwie. Odporność na ścieranie to ich najważniejszy atut. Poza tym mają specjalnie ukształtowany spód, który ułatwia odprowadzanie nadmiaru wody.
Inne wycieraczki zewnętrzne, to wycieraczki szczotkowe wykonane z twardego tworzywa. Dostępne są w rolkach, zwykle o szerokości 1m i różnych kolorach. Mogą być przycięte do dowolnych wymiarów. Wycieraczki szczotkowe dzięki chropowatej powierzchni dobrze usuwają brud, starannie oczyszczając każdy rodzaj podeszwy. Na zewnętrzne wycieraczki nadają się też wycieraczki na podkładzie gumowym odzyskiwanym z recyclingu. Zużyte opony samochodowe są często wykorzystywanym do tego surowcem, który przetworzony (przetapianie), daje gumowy materiał. Jest on pokrywany dekoracyjnymi wzorami i malowany. Ostatecznie powstaje wycieraczka wyglądająca jak artystyczny obraz na gumowym podkładzie. Jest ona odporna na plamy i odbarwienia. Doskonale usuwa się z niej wszelkie zanieczyszczenia. Zachowuje oryginalne kolory przez długi czas8.
1 za https://pl.wikipedia.org/wiki/Wycieraczka_(do_butów)
2 tamże
3 za http://www.pomorska.pl/artykuly-sponsorowane/a/stomil-100-lat-z-bydgoszcza,13206708/
4 za http://blog.ultimatemats.com/2013/draft-the-crazy-history-of-floor-mats/
5 za „Historia polskiego przemysłu gumowego karty z historii polskiego przemysłu chemicznego” Stowarzyszenie Inżynierów i Techników Przemysłu Chemicznego
6 tamże
8 tamże